AI + Machine Learning, Industry trends, Microsoft Azure portal
Azure high-performance computing leads to developing amazing products at Microsoft Surface
Posted on
4 min read
This blog was written in collaboration with the Microsoft Surface and Azure team. It describes how we used Azure high-performance computing (HPC) to save time, costs, and revolutionized our product design piece of manufacturing our Microsoft Surface products.
The Microsoft Surface organization exists to create iconic end-to-end experiences across hardware, software, and services that people love to use every day. We believe that products are a reflection of the people who build them, and that the right tools and infrastructure can complement the talent and passion of designers and engineers to deliver innovative products. Product level simulation models are routinely used in day-to-day decision making on design, reliability, and product features. The organization is also on a multi-year journey to deliver differentiated products in a highly efficient manner. Microsoft Azure HPC plays a vital role in enabling this vision. Below is an account of how we were able to do more with less by leveraging the power of simulation and Azure HPC.
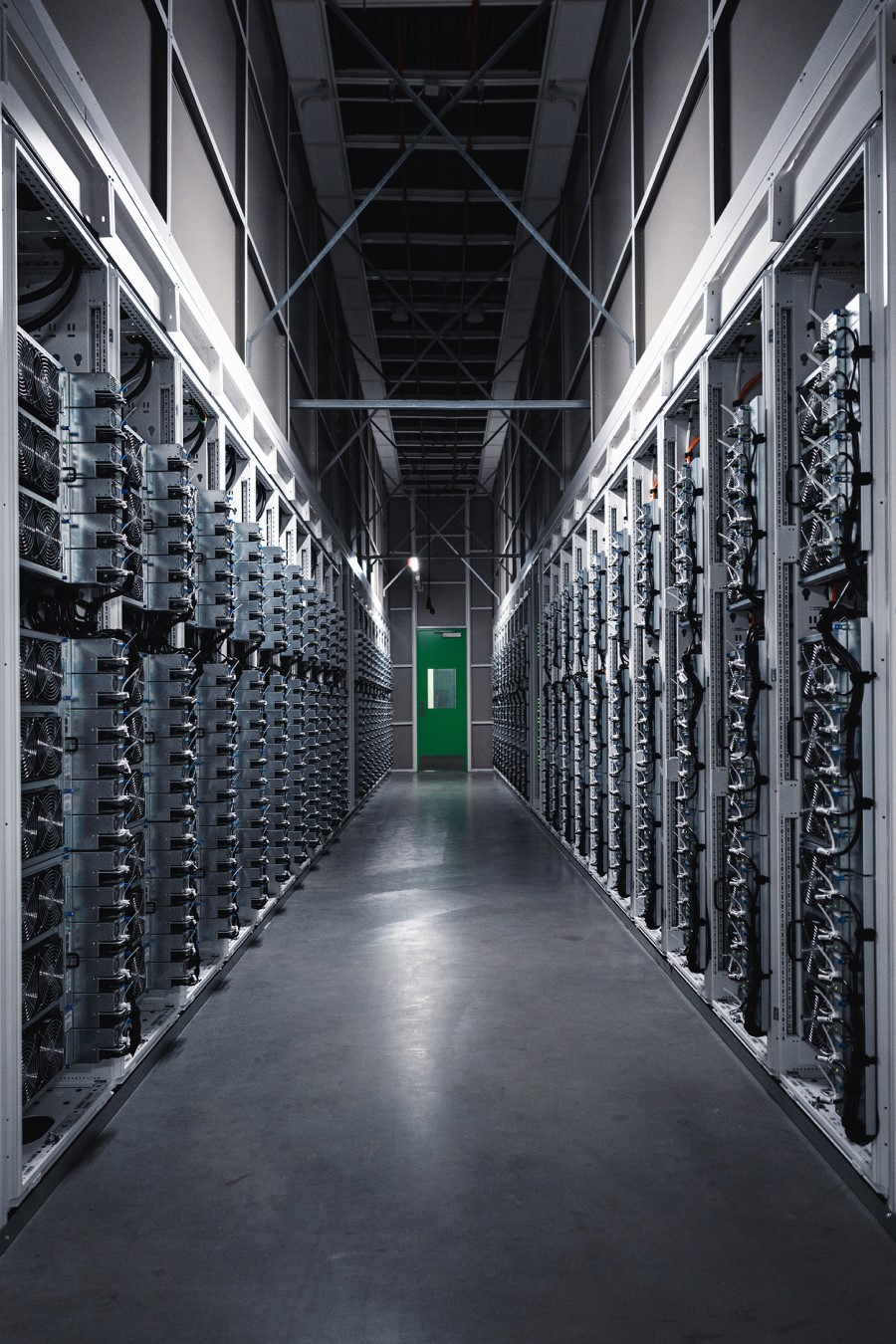
Surface devices development on Microsoft Azure
I’m a Principal Engineer at Microsoft and a structural analyst. I’ve been a heavy user of Azure HPC and an early adopter of Azure A8 and A9 virtual machines. In 2015, with the help of our Surface IT team, we deployed and solved many issues with Abaqus (a Finite Element Analysis (FEA) software) implementation in Azure HPC. By 2016, product level structural simulations for Surface Pro 4 and the original Surface laptop had fully migrated to Azure HPC from on-premises servers. Large models with millions of degrees of freedom became routine and easily solved on Azure HPC. This early use of simulations enabled problem solving for design engineers tasked with robustness and reliability metrics. Usage grew along with product line growth. Along with my colleagues Pritul Shah, Senior Director of a cross product engineering team, and Jarkko Sihvonen, Senior Engineer of the IT Infrastructure and Services team, we collaborated to scale up structural simulation footprint in our organization. The vision to build a global simulation team meant access to computing servers in Western North America and Southeast Asia which was easily deployed by the Surface IT and Azure HPC teams.
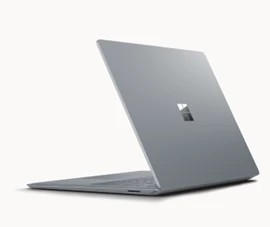
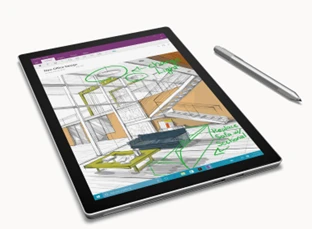
Product development: Surface laptop
The availability of Azure HPC for structural simulations using Abaqus helped make this a primary development tool for product design. Design concepts created in digital computer-aided design (CAD) systems are translated into FEA model in detail. These are true digital prototypes and constitute all major subsystems in the device. The analyst can use FEA models to impose different test and reliability conditions in a virtual environment and determine feasibility. In a few days, hundreds of simulations are executed to evaluate various design ideas and solutions to make the device robust. Subsequently, the selected design becomes a protype and then subject to rigorous testing for real-world use conditions. There are multiple feedback loops built into our engineering process to compare actual tests and FEA results for model validation.
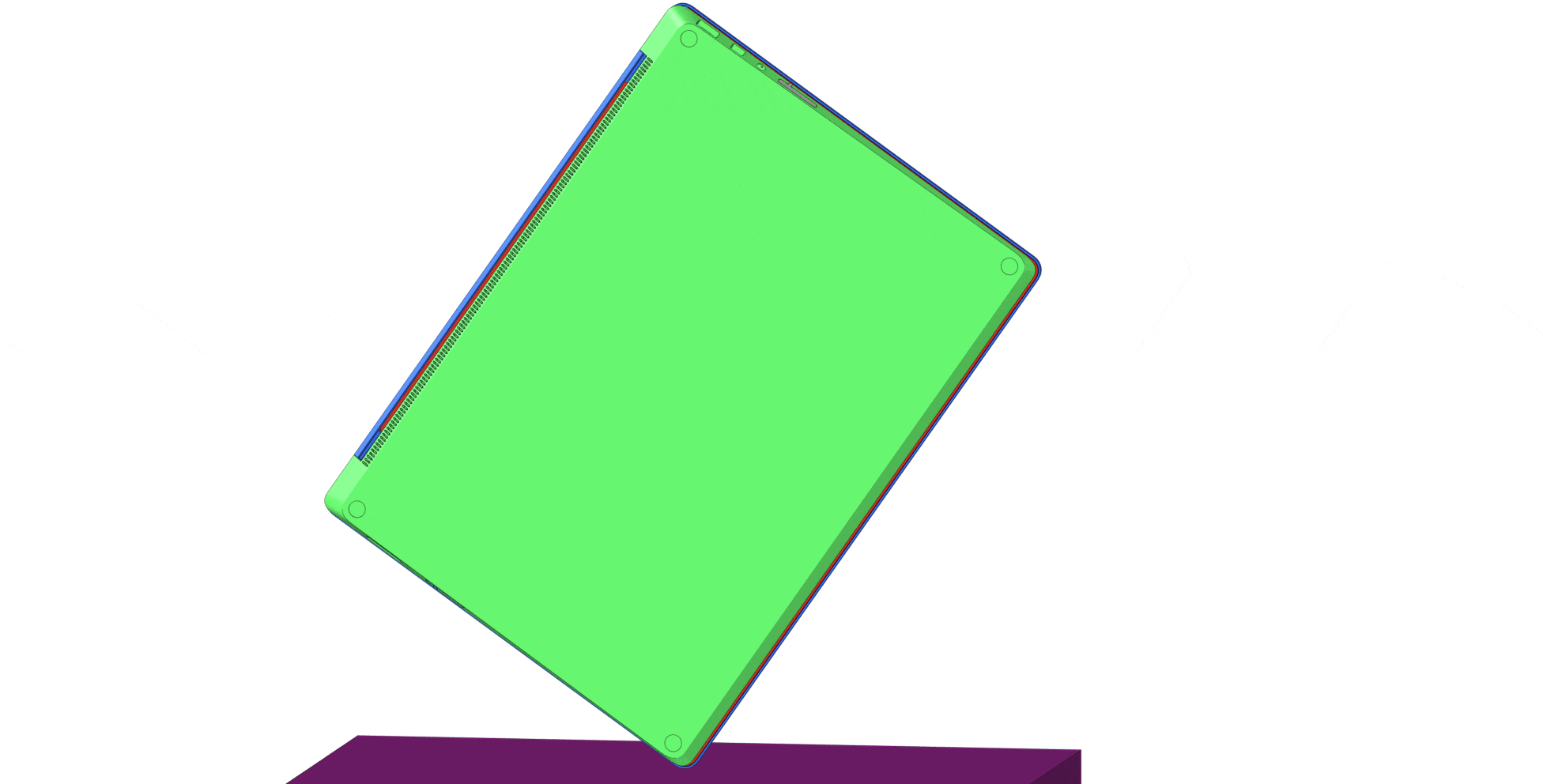
In the first graphics depicted above, a digital prototype (FEA model) laptop device is set-up to drop on its corner to the floor. This models the real-world physical testing that is conducted in our Reliability Engineering labs. The impact velocity for a given height is the initial condition for the dynamic simulation. The dynamic drop simulation is executed on hundreds of cores of an Azure HPC cluster using Abaqus solver. We used the Abaqus and Explicit solver which is known for its robust and accurate solution for high-speed, nonlinear, dynamic events such as consumer electronics drop testing and automotive crashworthiness. These solvers are optimized especially for Azure HPC clusters and enable scaling to thousands of cores for fast throughputs. The simulation jobs complete in a matter of a few hours on these optimized Azure HPC servers instead of the days it used to take previously. The results are reviewed by the analysts and stress levels are checked against material limits. Design teams and analysts then review the reports and make design updates. This cycle continues in very quick loops as the Azure HPC servers enable fast turnaround for reviews.
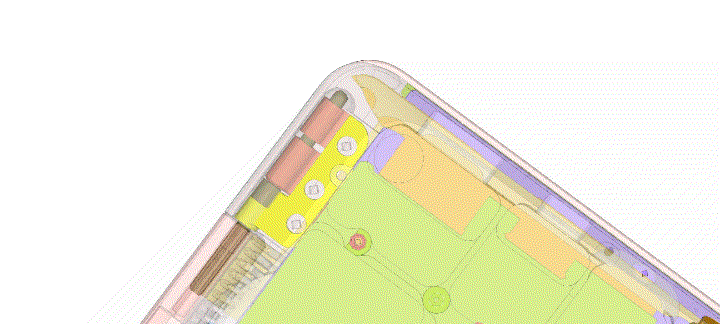
The second graphic depicts an example of the hinge in the device that was optimized for strength. The team was able to visualize the impact induced motion and stress levels of the hinge internal parts from the simulation. This enabled us to isolate the main issue and make the right design improvements. This insight helped redesign the hinge assembly to cause lower stress levels. Significant time was saved in the design process as only one iteration was needed for success. Tooling, physical prototyping, and testing costs were also saved.
Presently, the entire Microsoft Surface product line utilizes this approach of validating design with digital prototypes (FEA models) run on Azure HPC clusters. Thousands of simulation jobs are executed routinely in a matter of weeks to enable cutting-edge designs that have very high reliability and customer satisfaction.
What’s next
The team is now focused on deploying more scalable simulation and Azure HPC resource for multi-disciplinary teams and for multi-physics modeling. There is a huge opportunity to enable machine learning and AI in product creation. Azure HPC and the partnerships within Microsoft organizations will be leveraged to drive large scale innovations at a rapid speed. We are also continuing this digital transformation journey with model based systems engineering (MBSE) with the V4 Institute. World-class organizations looking to do more with less and on a quest for scaling digital simulations will greatly benefit from collaborating with Azure.
Learn More
- Learn more about Azure HPC.
- Get the latest Azure HPC content.
- Find out how Microsoft Cloud for Manufacturing can help you embrace new design and manufacturing paradigms.